查看完整案例

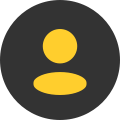

收藏

下载
总部位于布里斯托和伦敦的事务所Automated Architecture Ltd (AUAR)于近期完成了他们的第一个永久性居住单元设计:音乐家之屋。这座小屋占地10平方米,采用AUAR自己的模块化木材建筑系统建造。该系统整合了机器人和自动化技术,旨在提供高质量、设计精美且可持续的经济适用住房。此外,该项目还展示了AUAR系统在支持定制化设计和鼓励社区参与建造过程方面的潜力。
Bristol and London-based design and technology company Automated Architecture Ltd (AUAR) has completed its first permanent dwelling unit: Dwelling Unit for Musicians. At 10 square metres (107 square feet), the dwelling unit is constructed using AUAR’s modular timber building system, which integrates robotics and automation to provide high-quality, beautifully designed, and sustainable affordable housing. In particular, the project demonstrates the potential of AUAR’s system to support customisation and community participation in the construction process.
▼建筑外观,Exterior view
该项目的业主是布里斯托的两位音乐家,他们分别演奏大提琴和低音提琴。业主们希望将小屋作为办公室和排练空间使用,而AUAR的系统刚好能够满足他们对依据场地和功能定制特殊居住单元的需要。小屋可以在保证充足采光的前提下实现隔热和隔音,同时维持可再生的特性与低碳足迹。
Based in Bristol, the clients for Dwelling Unit for Musicians are a cellist and double bassist who will use the space as an office and rehearsal studio. They selected AUAR’s system over other backyard-unit options because AUAR’s dwelling units can be easily customized to site and use, offering a unique structure. They also feature thermal and acoustic insulation, which can be achieved while still retaining a light-filled space, as well as renewable properties and a low-carbon footprint.
▼室内概览,Interior view
作为小屋的核心,AUAR的模块化系统由可再生木材制成,可通过机器人预制并组装为居住单元。在生产过程中,机器人先将木板组装为独立的建筑模块,随后再将这些模块堆叠为易于运输的单元。在运送到指定地点后,这些单元将由当地工匠和施工方装配为最终的住宅。
利用AUAR的自动化流程,这些单元可以非常方便地根据场地特征和居住者个人的生活方式以及视觉偏好进行定制。这为当下千篇一律且难以适应当地环境的模块化住房设计提供了一种截然不同的替代方案。更为特殊的是,这些木制的建筑模块可以根据新的用途进行拆卸和重新组装,因而减少了材料的浪费,符合循环设计的原则。
At its core, AUAR’s modular system consists of building blocks made from timber, a renewable material, which are robotically pre-fabricated and assembled into dwelling units. The production chain begins when a robot assembles timber sheets into individual building blocks, then stacks the blocks into easily transportable units. These units are delivered locally to a given site and assembled by local craftspeople and builders into homes.
Using AUAR’s automation process, the units can be easily customized based on site characteristics and a given inhabitant’s lifestyle and visual preferences. This provides a radical alternative to existing modular housing approaches which are repetitive and difficult to adapt to local contexts. Uniquely, the timber building blocks can be disassembled and reassembled for other uses, therefore creating less material waste and aligning with principles of circular design.
▼AUAR的模块化系统由可再生木材制成
AUAR’s modular system consists of building blocks made from timber
▼开阔的落地窗为小屋与花园建立了视觉和物理上的连接
A large floor-to-ceiling window/door offers a visual and physical connection to the client’s garden
在该项目中,AUAR针对建筑场地的东南朝向以及客户的需求提出了多种设计方案。AUAR首席执行官Mollie Claypool对此表示:“这些方案中有些较为内敛,有些则更加开放,还有一些则探讨了创建凹室空间和安装天窗的可能性。在这个基础上,业主选出了他们更喜欢的做法,最终让小屋得以落成。更重要的是,由于项目使用的模块数量是确定的,因此具体所要花费的成本在每个阶段都是已知的。”
In the case of Dwelling Unit for Musicians, AUAR generated multiple designs in response to the South-East facing building site and an understanding of the clients’ needs. With the same number of blocks, AUAR discussed radically different, customised options. “Some of the designs were more introverted, other block combinations were more open to the garden, whilst others explored the design possibilities of an alcove space, with or without rooflight, and so on,” explains AUAR CEO Mollie Claypool. From there, the clients selected the features they preferred, and a final version was generated. Importantly, the exact cost was known at all times, as it relates directly to the number of blocks used.
▼工作空间,Working space
木制单元的生产是在布里斯托当地的制造中心“KWMC The Factory”完成的。模块的预制花费了两周时间,住宅单元的装配则由当地承包商和具有相关建造经验的社区居民与AUAR的团队历时7天完成。
Fabrication of the timber components took place locally, in Bristol, at the citizen-led manufacturing hub KWMC The Factory. Block prefabrication took two weeks and the dwelling unit itself was constructed in seven days by a combination of local contractors and community residents experienced in working with AUAR’s modular building system and employed to work alongside the AUAR team.
▼办公桌上方的天窗进一步引入了自然光线
A skylight positioned over the desk enhances the natural light flooding the unit
完成后的小屋与业主的后院空间形成了无缝对接。虽然建筑的占地面积不大,但其开阔的落地窗为小屋与花园建立了视觉和物理上的连接,营造出通透宽敞的感觉。办公桌上方的天窗进一步引入了自然光线。除了木制模块和木质包层,建筑中使用的所有材料都是根据其低碳和可持续的特性而选择的,其中包括无毒且可回收的EPDM屋顶、橡胶地面以及纸纤维素绝缘层等。
总体而言,AUAR的建造系统使用了可持续的材料,并通过制造和施工过程的本地化实现了控制力的分散,无需再从遥远的地区进口材料和模块化的住宅。这种做法也能起到减少碳足迹和增加社区参与的作用。
The resulting unit fits seamlessly into the client’s backyard. Despite a small footprint of 10sqm (107sf), a large floor-to-ceiling window/door offers a visual and physical connection to the client’s garden, giving an impression of spaciousness. A skylight positioned over the desk enhances the natural light flooding the unit. Along with the timber blocks and timber cladding, all additional construction materials were selected for their low-carbon, sustainable properties. These include a non-toxic, recyclable EPDM roof, rubber floor, and paper cellulose insulation.
Overall, AUAR’s system uses sustainable materials and decentralizes by localizing the fabrication and construction process, instead of importing materials or modular homes from far afield. This simultaneously reduces carbon footprint and increases community involvement.
▼小屋与业主的后院空间形成了无缝对接,The resulting unit fits seamlessly into the client’s backyard
▼夜景,Night view
▼建筑细节,Detailed view
AUAR的下一个居住单元将于2021年12月底完工,将展示从小型(10-15平方米)、中型(15-25平方米)到大型(25-50平方米)的不同配置。AUAR的系统提供了社区需要的、能够对日常生活产生积极影响的居住环境。
The next in AUAR’s series of Dwelling Units is due for completion by the end of December 2021 and showcases a different configuration of blocks. Scaling from small (10-15sqm/107-160sf), through to medium (15-25sqm/160-270sf) and large (25-50sqm/270-540sf), AUAR’s system offers housing that communities need at scales that positively impact daily lives.
▼平面图,Plan
▼剖面图A,Section A
▼剖面图B,Section B
Project credits:
Design: Automated Architecture (AUAR Ltd); Team: Gilles Retsin, Mollie Claypool, Kevin Saey, Ivo Tedbury
Square footage: 10m2
Program: Workspace
Materials: Timber block, timber cladding, EPDM roof, rubber floor, paper cellulose insulation
Photography: naaro